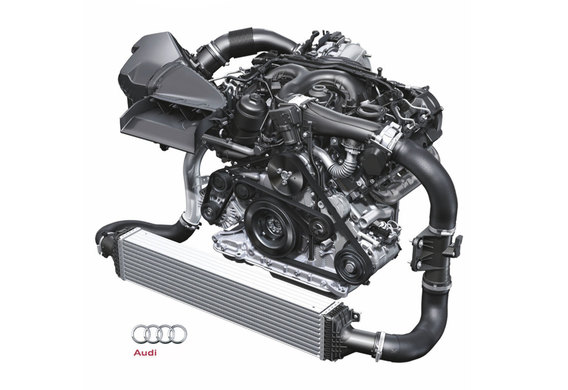
Geschichte der Konstruktion von Turbodieselmotoren
Die Turbolader wurden eingesetzt, um die Leistung von Verbrennungsmotoren noch in der Entwicklungsphase dieser Technologie zu erhöhen. Im Jahr 1911 spielte ein von einem Amerikaner patentierter Turbolader, der am Anfang seiner Entwicklung stand, eine bedeutende Rolle bei den militärischen luftfahrtgebrandeten Benzinmotoren, die auf Kampfflugzeuge und Bomber gesetzt wurden, um ihre Höhe zu verbessern. Die Technologie wurde vor kurzem in der Automobildyslexia eingesetzt. Der erste Serienwagen mit Turbodiesel wurde 1978 eingeführt. Mercedes-Benz 300 SD, und 1981 wurde es von VW Turbodiesel gefolgt.
Geräte-und Betriebsprinzip eines Turbodieselmotors
Das Betriebsprinzip des Dieselmotors basiert auf Abgas. Nach Verlassen des Zylinders gelangen die Abgase in die Netzhaut der Turbine, drehen sie und die Turbine des Verdichters wird in den Luftstrom in die Zylinder eingebaut.
So haben Turbkompressoren im Gegensatz zu Atmosphärendieseln bei höherem Druck Druckluft in die Zylinder. Dadurch steigt das Volumen der in einem Zyklus in den Zylinder eintretenden Luft. In Kombination mit einer Erhöhung des Volumens des brennenden Brennstoffs (die Anteile der Fuel-Luft-Mischung bleiben unverändert), ergibt sich eine Erhöhung der Kapazität bis zu 25%.
Um das Volumen der Ansaugluft weiter zu erhöhen, wird auch ein Zwischenkühler verwendet, wobei eine spezielle Vorrichtung die atmosphärische Luft vor dem Motor abkühlt. In der Physik ist bekannt, dass kalte Luft weniger als warm ist. So kann die Kühlung mehr Luft über den Kreislauf in den Zylinder "schieben".
Dies hat zur Folge, dass die Turbine weniger spezifischen Kraftstoffverbrauch (in Gramm pro Kilowattstunde) und eine höhere Kapazität (die Anzahl der Pferdestärken pro Liter Hubraum) aufweist. All dies ermöglicht es, die Gesamtleistung des Motors deutlich anzuheben, ohne die Größe und die Anzahl der Umdrehungen deutlich zu erhöhen.
Plus-und Minus-Dieselmotor mit Turboaufladung
Die umgekehrte Seite der Erhöhung der Leistung des Motors unter Beibehaltung der gemeinsamen Eigenschaften, d. h. der forciertere Verschleiß der Knoten, als Folge, eine Verringerung der Kraftwerksressource. Darüber hinaus erfordern Turbinen spezielle Motorenöle und die strikte Einhaltung der empfohlenen Servicezeiträume des Herstellers. Der Luftfilter ist noch anspruchsvoller. Darüber hinaus kann die Turbine von Niederdruckturbinen einen Turboyama-Effekt haben, der sich in dem auffälligen "Essen" bei niedrigen und mittleren Motordrehzahlen niederschlägt.
Turbierte Motoren sind weniger sparsam als atmosphärischer Diesel, und sie verbrauchen 20 bis 50% mehr Treibstoff auf dem gleichen Volumen. Ein weiterer offensichtlicher Nachteil des Turbo-Boost-Systems ist, dass er sehr empfindlich auf den Verschleiß der Kolbengruppe reagiert. Durch die Erhöhung des Drucks der Kurbelgehäusegase wird die Turbinenressource reduziert. Unter solchen Bedingungen gibt es ein "Ölfasten" und ein Bruch des Turboladers. Der Schaden an dieser Einheit kann durchaus zum Ausfall des gesamten Motors führen, während die Turbo-Dieselmotoren noch weniger machtvoll sind als ihre stimmungsvollen Brüder.
Im Allgemeinen ist die Anwesenheit eines technisch komplexen Turboladers, der zusätzliche Druckstabilisierungsvorrichtungen erfordert, Notentladung, und so weiter macht die Kraftinstallation des Autos anspruchsvoller, die Anzahl der Teile zu erhöhen, wodurch die Gesamtzuverlässigkeit reduziert wird. Darüber hinaus ist die Ressource des Turboladers selbst viel kleiner als die des Motors als Ganzes.
Moderne Diesel-Motorenverbesserungen
Das System zur Steigerung der Effizienz und Flexibilität des Diesel-Modus als "Common-Rail" hat heute beachtliche Popularität erlangt. Wenn bei dem herkömmlichen Dieselmotor jeder Hochdruckpumpenabschnitt in einer separaten Kraftstoffleitung mit Kraftstoff versorgt wird, der pro Injektor geschlossen ist. Auch wenn die Dicke der Kraftstoffleitungen etwas anders ist, wenn sie in der Atmosphäre von 1500-2000 unter Druck gesetzt werden, sind sie leicht, aber "aufgebläht". Dadurch unterscheidet sich der in den Zylinder 1 fallende Anteil des Kraftstoffes von dem berechneten Brennstoff. "Dovesook" erhöht den Kraftstoffverbrauch, erhöht die Opazität und reduziert die vollständige Verbrennung des Fuel-Luft-Gemisches.
Eine gute Engineering-Lösung für dieses Problem wurde gleichzeitig von mehreren Automobilherstellern entwickelt. In dem neuen System pumpt die Hochdruck-Kraftstoffpumpe Kraftstoff in die gemeinsame Kraftstoffschiene, die unter anderem die Rolle eines Widerfahrers, also eines Druckstabilisators im Pfad, spielt. In der Rampe gibt es immer eine konstante Menge an Kraftstoff, die nicht unter dem pulsierenden Druck steht, sondern unter konstantem Druck.
Darüber hinaus hat die Entwicklung intelligenter Technologien elektronische Öffnungssysteme ermöglicht (in traditionellen Dieselmotoren werden Einspritzzyklen mechanisch durch den zunehmenden Druck in der Pipeline gesteuert). Die elektronische Einheit, die die Leistung der Düsen steuert, berücksichtigt Informationen über die Stellung des Gaspedals, den Druck in der Rampe, die Motortemperatur, die Last auf dem Motor usw. Auf der Grundlage dieser Daten wird der Kraftstoffanteil des Kraftstoffs berechnet und zugeführt.
Eine weitere Neuerung, die durch die Entwicklung der Fahrzeugelektronik eingeführt wird, ist ein zweistufiger Kraftstoffzulauf in den Brennraum. Zuerst suchen wir nach einem "Split" (um ein Milligramm). Wenn die Verbrennung zu der Wirkung der Kompression hinzugefügt wird, erhöht die Temperatur in der Kammer, und die Hauptdosis injiziert mit der Spur verbrennt mehr glatt, auch die Erhöhung des Drucks in dem Zylinder. Dadurch wirkt der Motor weicher und weniger geräuschlos, während der Kraftstoffverbrauch um etwa 20% reduziert wird, während das Drehmoment um 25% erhöht wird. Wichtig ist, den Ruß in den Auspuff zu reduzieren.
Unter den neuen Entwicklungen zur Verbesserung der Umweltleistung der Dieselmotoren bei der Optimierung ihrer Wirtschaftlichkeit ist BlueTec das erfolgversprechendste System, das die Spezialisten der Daimler AG entwickelt haben. Der größte Teil davon ist ein innovatives Verfahren zur katalytischen Reduktion von Abgas.
Katalysatoren moderner Fahrzeuge arbeiten auf Kosten keramischer oder metallischer "Wabenkörper", die mit einer Schicht reaktiver Substanzen-Katalysatoren bedeckt sind. Katalysator oxidiert oder restaurieren toxische Verbindungen von CO, CH und NOx zu Kohlendioxid, einfachem Stickstoff und Wasser.
Allerdings sind die Eigenheiten von Dieselkraftstoff sowie die Prozesse der Entstehung und Verbrennung des Fuel-Luft-Gemisches in Dieselöl so, dass der Auspuff nicht nur schädliche chemische Komponenten, sondern eine große Menge Ruß enthält. Außerdem erhöht sich der Anteil der NOx-Anstiege, wenn man beginnt, den Anteil des Rußanteils zu reduzieren, und umgekehrt. So ist für die komplexe Behandlung von Diesel-Exhas ein Mehrkomponenten-Chemiker erforderlich, ein mechanisches System, das den Bau eines Autos erschwert und infolgedessen die Rentabilität der Produktion verringert.
Die BlueTec-Technologie basiert auf einer Kombination aus traditionellen und neuen Lösungen. Das Abgas hat begonnen, den Widerstand der Mehrheit der Diesel-Fahrzeuge und den Katalysator für "Töten" Kohlenstoff zu passieren. Anschließend wird die Abgaseinspritzung mit einem Aktivreagenz AdVlue auf Basis von Harnstoff (Ammoniaklösung in Wasser) besprüht. Die resultierende Mischung wird in einen speziellen Wahl-Katalysator (SCR), wo Ammoniak aus AdBlue unter dem Einfluss der Katalyse bei 250-300 ° C ist in der chemischen Reaktion der Stickoxide durch "Einnahme" sie zu Stickstoff und Wasser. Der Rest der schädlichen Komponenten wird hier verbrannt.
BlueTec hat mit offensichtlichen Pros keine weniger offensichtlichen Nachteile. Für den Speicher einer AdLog-Komponente ist eine separate Kapazität erforderlich. Das System selbst ist durch die Anwesenheit von zusätzlichen Hubs und Autobahnen kompliziert. Darüber hinaus ist das System noch lustvoller auf die Qualität von Kraftstoffen und kann nur mit einem minimalen Schwefelgehalt von Salzen betrieben werden.
Ein weiteres sehr relevantes Problem für Russland-die Lösung von Adlue wird bei minus 11,5 Grad gemessen. BlueTec-Ingenieure arbeiten nun aktiv an der Verbesserung der Systeme, ohne Harnstoff zu verwenden. Heute ist die Prüfung und Verfeinerung des Verbundfilters, Platinkatalysator-Katalysators und zweier SCR-Katalysatoren ausschließlich für Stickoxide. Das System erlaubt derzeit die Verwendung von NOx in Dieselabgasen bei etwa Euro 5.