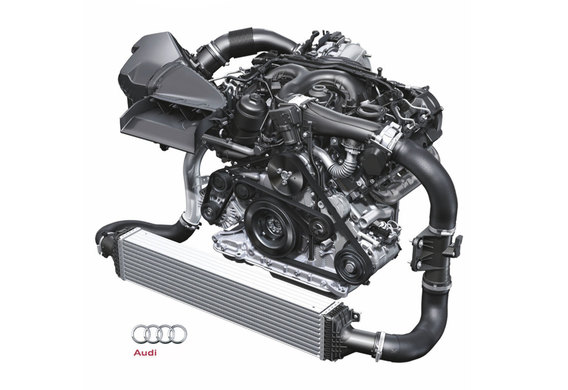
Historia budowy turbodoładowanych silników Diesla
Turbosprężarki zostały wykorzystane do zwiększenia mocy silników spalinowych jeszcze w fazie rozwojowej tego typu technologii. W 1911 roku, turbosprężarka opatentowana przez Amerykanina, o świcie swojego rozwoju, odegrała znaczącą rolę w wojskowym lotnictwie-silniki benzynowe zostały umieszczone na myśliwce i bombowce, aby poprawić ich wysokość. Technologia została ostatnio wykorzystana w samochodowym dysleksji. Pierwszy seryjny samochód z turbo diesel został wprowadzony w 1978 roku. Mercedes-Benz 300 SD, a w 1981 roku odbyła się w nim VW Turbodiesel.
Urządzenie i zasada działania turbodoładowanego silnika wysokoprężnego
Zasada działania silnika wysokoprężnego opiera się na spalinach. Opuszczając butlę, gazy spalinowe wchodzą do siatkówki turbiny, obracają ją i turbiną sprężarki wbudowanej w przepływ powietrza do cylindrów.
W ten sposób, w przeciwieństwie do diesli atmosferycznych, turbsprężarki wywierały presję powietrza na butle pod wyższym ciśnieniem. W związku z tym zwiększa się objętość powietrza wchodząca do butli w jednym cyklu. W połączeniu ze wzrostem objętości palącego się paliwa (proporcje mieszanki paliwowo-powietrznej pozostają niezmienione) daje to wzrost wydajności do 25%.
Aby jeszcze bardziej zwiększyć objętość powietrza dolotowego, stosuje się również intercooler, specjalne urządzenie chłodzące powietrze atmosferyczne przed silnikiem. W fizyce wiadomo, że zimne powietrze jest mniejsze niż ciepłe. W ten sposób, chłodnictwo może "wcisnąć" do cylindra więcej powietrza w cyklu.
W rezultacie turbina ma mniejsze zużycie paliwa specyficznego (w gramach na kilowatogodzinę) oraz większą moc obliczeniową (ilość mocy KM na litr mocy silnika). Wszystko to umożliwia znaczne podniesienie całkowitej mocy silnika bez znacznego zwiększenia jego wielkości i liczby obrotów.
Plus i minus silnik diesla z turbodoładowaniem
Odwrotna strona wzrostu mocy silnika przy zachowaniu wspólnych cech, czyli wymuszanie-bardziej intensywne zużycie węzłów, w konsekwencji, zmniejszenie zasobności elektrowni. Ponadto turbiny wymagają specjalnych rodzajów olejów silnikowych i ścisłego przylegania do zalecanych przez producenta okresów obsługi. Filtr powietrza jest jeszcze bardziej wymagający. Ponadto turbina turbin o niskim ciśnieniu może mieć efekt turboama, co znajduje odzwierciedlenie w zauważalnym "jedzeniu" przy niskich i średnich prędkościach silnika.
Silniki turbowane są mniej ekonomiczne od atmosferycznego oleju napędowego, pochłaniamy od 20 do 50% więcej paliwa na tym samym wolumenie. Kolejną oczywistą wadą systemu turbo-boost jest fakt, że jest on bardzo wrażliwy na zużycie grupy tłoków. Zwiększenie ciśnienia gazów ze skrzyni korbowej zmniejsza zasobność turbiny. W takich warunkach znajduje się "olejek na czczo" i łamanie turbosprężarki. Uszkodzenie tej jednostki może dobrze doprowadzić do awarii całego silnika, podczas gdy turbo silniki wysokoprężne są jeszcze mniej okaleczające niż ich atmosferycznych braci.
Generalnie, obecność technicznie skomplikowanej turbosprężarki, która wymaga dodatkowych urządzeń do stabilizacji ciśnienia, rozładowania awaryjnego, i tak dalej sprawia, że instalacja zasilania samochodu jest bardziej wyrafinowana, zwiększając liczbę części, zmniejszając tym samym ogólną niezawodność. Dodatkowo, zasób samej turbosprężarki jest znacznie mniejszy niż w przypadku silnika jako całości.
Nowoczesne ulepszenia silnika Diesla
System zwiększający wydajność i elastyczność trybu diesla jako "Common-Rail" zyskał dziś znaczną popularność. Jeżeli w tradycyjnym silniku wysokoprężnym, każda sekcja pompy wysokociśnieniowej jest dostarczana z paliwem w oddzielnej linii paliwowej, która jest zamknięta dla każdego wtryskiwacza. Mimo, że grubość linii paliwowych jest nieco inna, gdy są one pod ciśnieniem w 1500-2000 atmosfera, są one lekko, ale "napompowane". W związku z tym, porcja paliwa wpadającego do butli różni się od obliczonego paliwa. "Dovesook" zwiększa zużycie paliwa, zwiększa zmętnienie i redukuje całkowite spalanie mieszanki paliwowo-powietrznej.
Dobre rozwiązanie inżynieryjne do tego problemu zostało opracowane jednocześnie przez kilku automakerów. W nowym systemie wysokociśnieniowa pompa paliwa pompuje paliwo do wspólnej szyny paliwowej, która między innymi odgrywa rolę rezystory, czyli stabilizatora ciśnienia w ścieżce. W rampie zawsze jest stała ilość paliwa, która nie znajduje się pod ciśnieniem pulsującym, ale pod stałą presją.
Ponadto, rozwój inteligentnych technologii umożliwił elektroniczne systemy otwierania (w tradycyjnych diesle, cykle wtrysku są sterowane mechanicznie poprzez zwiększenie ciśnienia w rurociągu). Jednostka elektroniczna, która steruje wydajnością dysz, bierze pod uwagę informacje dotyczące pozycji pedału przyspieszenia, ciśnienia w rampie, temperatury silnika, obciążenia silnika itp. Na podstawie tych danych należy obliczyć i nakarmić część paliwa w paliwie.
Kolejną nowością wprowadzoną przez rozwój elektroniki samochodowej jest dwustopniowe zasianie paliwem w komorze spalania. Po pierwsze, szukamy "rozdwojenia" (około miligrama). Po dodaniu spalania do efektu sprężania zwiększa się temperatura w komorze, a główna dawka wtryskiwana wraz ze śladem opara się bardziej płynnie, także zwiększając ciśnienie w cylindrze. W rezultacie silnik pracuje bardziej miękko i mniej głośno, podczas gdy zużycie paliwa zmniejsza się o około 20%, podczas gdy moment obrotowy jest zwiększany o 25%. Co ważne, zmniejsza się sadza w spalinach.
Wśród nowości zaprojektowanych w celu poprawy efektywności środowiskowej diesli przy jednoczesnej optymalizacji ich gospodarki, BlueTec jest najbardziej obiecującym systemem opracowanym przez specjalistów Daimler AG. Główną jego częścią jest innowacyjna procedura katalitycznego redukcji spalin.
Katalizatory współczesnych pojazdów pracują kosztem ceramiki lub metalicznego "plastra miodu", pokrytych warstwą substancji reaktywnych-katalizatorów. Katalizatory utleniaczy lub przywracają toksyczne związki CO, CH i NOx do dwutlenku węgla, prostego azotu i wody.
Jednakże specyfikę oleju napędowego, jak również procesy powstawania i spalania mieszanki paliwowo-powietrznej w oleju napędowego są takie, że spaliny zawierają nie tylko szkodliwe składniki chemiczne, ale dużą ilość sadzy. Co więcej, jeśli zaczniesz obniżać udział sadzy, zawartość NOx wzrasta, i odwrotnie. Tak więc, dla kompleksowego leczenia oleju napędowego, potrzebny jest wieloskładowy chemik, układ mechaniczny, który komplikuje budowę samochodu, a w konsekwencji zmniejsza opłacalność produkcji.
Technologia BlueTec zbudowana jest w oparciu o połączenie tradycyjnych i nowych rozwiązań. Spaliny zaczęły przejeżdżać przez opór większości pojazdów z silnikami wysokoprężnymi i katalizator do "zabijania" węgla. Następnie wtrysk jest rozpylany aktywnym odczynnikiem AdVlue w oparciu o mocznik (roztwór amoniaku w wodzie). Otrzymana mieszanina jest umieszczana w specjalnym katalizatorze wyborczym (SCR), gdzie amoniak z AdBlue pod wpływem katalizatora w temperaturze 250-300 ° C jest skuteczny w reakcji chemicznej tlenków azotu poprzez "zabranie" ich do azotu i wody. Reszta szkodliwych składników jest tu spalana.
Z oczywistych pros, BlueTec nie ma mniej oczywistych wad. Sklep komponentu AdLog wymaga oddzielnej mocy obliczeniowej. Sam system jest skomplikowany dzięki obecności dodatkowych koncentratorów i autostrad. Ponadto system jest jeszcze bardziej lustny dla jakości paliwa i może działać tylko na solenie z minimalną zawartością siarki.
Kolejny bardzo istotny problem dla Rosji-rozwiązanie Adlue jest mierzone na minus 11.5 stopni. Dlatego inżynierowie z firmy BlueTec aktywnie pracują nad poprawą systemów bez użycia mocznika. Obecnie jest to badanie i dopracowanie filtra kompozytowego, katalizatora platynowego katalizatora i dwóch SCR-katalizatorów wyłącznie do tlenków azotu. System obecnie pozwala na zastosowanie NOx w spalinach oleju napędowego na poziomie około Euro 5.