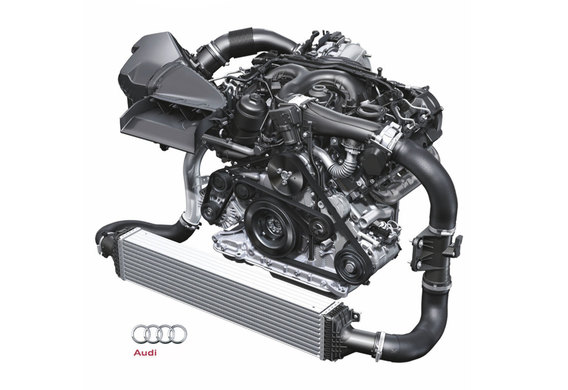
Historia de la construcción de motores diesel turboalimentados
Los turbocompresores se utilizaron para aumentar la potencia de los motores de combustión interna aún en fase de desarrollo de este tipo de tecnología. En 1911, un turbocompresor patentado por un estadounidense, en los albores de su desarrollo, jugó un papel significativo en los motores de gasolina de aviación militar que fueron colocados en aviones de combate y bombarderos para mejorar su altura. La tecnología se ha utilizado recientemente en la dislexia automotriz. El primer coche serie con un turbo diesel se introdujo en 1978. Mercedes-Benz 300 SD, y en 1981 Le siguió VW Turbodiesel.
Dispositivo y principio de funcionamiento de un motor diesel turboalimentado
El principio de funcionamiento del motor diesel se basa en el gas de escape. Dejando el cilindro, los gases de escape entran en la retina de la turbina, lo rotan y la turbina del compresor se construye en el flujo de aire en los cilindros.
Por lo tanto, en contraste con los dieseles atmosféricos, los turbcompresores tienen aire presurizado en los cilindros a mayor presión. Como resultado, el volumen de aire que entra en el cilindro en un ciclo es cada vez mayor. En combinación con un aumento en el volumen del combustible en llamas (las proporciones de la mezcla de combustible-aire permanecen sin cambios) esto da un aumento de la capacidad hasta un 25%.
Para aumentar aún más el volumen del aire de admisión, también se utiliza un intercooler, un dispositivo especial que enfría el aire atmosférico frente al motor. En la física, se sabe que el aire frío es menos que cálido. Por lo tanto, la refrigeración puede "empujar" al cilindro más aire durante el ciclo.
Como resultado, la turbina tiene un consumo de combustible menos específico (en gramos por kilovatio-hora) y mayor capacidad (el número de caballos de fuerza por litro de capacidad del motor). Todo esto permite elevar significativamente la potencia total del motor sin aumentar significativamente su tamaño y número de vueltas.
Motor diésel más y menos con turboalimentado
El lado inverso del aumento de la potencia del motor conservando al mismo tiempo las características comunes, es decir, el desgaste más intenso de los nudos, como consecuencia, una reducción del recurso de la central eléctrica. Además, las turbinas requieren tipos especiales de aceites de motor y una adherencia estricta a los períodos de servicio recomendados por el fabricante. El filtro de aire es aún más exigente. Además, la turbina de turbinas de baja presión puede tener un efecto turboyama, lo que se refleja en la notable "alimentación" a velocidades de motor bajas y medianas.
Los motores turbados son menos económicos que el diesel atmosférico, consumiendo entre 20 y 50% más de combustible en el mismo volumen. Otra desventaja obvia del sistema de turbo-boost es que es muy sensible al desgaste del grupo de pistones. Aumentar la presión de los gases del cárter reduce el recurso de la turbina. En tales condiciones hay un "ayuno de aceite" y la rotura del turbocompresor. El daño a esta unidad puede conducir a la falla de todo el motor, mientras que los motores diesel turbo son todavía menos mantenibles que sus hermanos atmosféricos.
En general, la presencia de un turbocompresor técnicamente complejo, que requiere dispositivos de estabilización de presión adicionales, descarga de emergencia, y así sucesivamente hace que la instalación de energía del coche sea más sofisticada, aumentando el número de piezas, reduciendo así la fiabilidad general. Además, el recurso del propio turbocompresor es mucho menor que el del motor en su conjunto.
Mejoras en el motor diesel moderno
El sistema de aumentar la eficiencia y flexibilidad del modo diesel como "Comon-Rail" ha ganado una considerable popularidad hoy en día. Si, en el motor diesel tradicional, cada sección de bomba de alta presión se suministra con combustible en una línea de combustible separada, que se cierra por inyector. A pesar de que el espesor de las líneas de combustible es ligeramente diferente cuando son presurizados en la atmósfera de 1500-2000, son ligeramente pero "inflados". Como resultado, la porcion del combustible que cae dentro del cilindro es diferente del combustible calculado. "Dovesook" aumenta el consumo de combustible, aumenta la opacidad y reduce la combustión completa de la mezcla de combustible y aire.
Una buena solución de ingeniería a este problema fue desarrollado simultáneamente por varios fabricantes de automóviles. En el nuevo sistema, la bomba de combustible de alta presión está bombeando combustible en el riel de combustible común, lo que, entre otras cosas, juega el papel de un resistor, es decir, un estabilizador de presión en el camino. En la rampa, siempre hay una cantidad constante de combustible que no está bajo la presión pulsante, pero bajo presión constante.
Además, el desarrollo de tecnologías inteligentes ha permitido sistemas de apertura electrónica (en los diesels tradicionales, los ciclos de inyección se controlan mecánicamente aumentando la presión en la tubería). La unidad electrónica, que controla el rendimiento de las boquillas, tendrá en cuenta la información sobre la posición del pedal del acelerador, la presión en la rampa, la temperatura del motor, la carga en el motor, etc. Sobre la base de estos datos, se calculará y alimentará la porción de combustible del combustible.
Otra novedad introducida por el desarrollo de la electrónica automotriz es la alimentación de combustible de dos etapas en la cámara de combustión. Primero, estamos buscando una "división" (alrededor de un miligramo). Cuando la combustión se añade al efecto de la compresión aumenta la temperatura en la cámara, y la dosis principal inyectada con el rastro quema más suavemente, aumentando también la presión en el cilindro. Como resultado, el motor funciona más suave y menos ruidoso, mientras que el consumo de combustible se reduce en aproximadamente un 20% mientras que el par se incrementa en un 25%. Lo importante es reducir el hollín en el escape.
Entre los nuevos desarrollos diseñados para mejorar el desempeño ambiental de los diesels mientras se optimiza su economía, BlueTec es el sistema más prometedor desarrollado por los especialistas de Daimler AG. La parte principal de la misma es un procedimiento innovador para la reducción catalítica del gas de escape.
Convertidores catalíticos de vehículos modernos funcionan a expensas de cerámica o "panal" metálico, cubierto con una capa de sustancias reactivas-catalizadores. El catalizador oxida o restaura compuestos tóxicos de CO, CH y NOx a dióxido de carbono, nitrógeno simple y agua.
Sin embargo, las peculiaridades del combustible diesel, así como los procesos de formación y combustión de la mezcla combustible-aire en el gasoil son tales que el escape contiene no sólo componentes químicos nocivos, sino una gran cantidad de hollín. Por otra parte, si usted comienza a reducir la cuota de hollín, el contenido de NOx aumenta, y viceversa. Así, para el complejo tratamiento de los exhas diesel, se necesita un químico multicomponente, un sistema mecánico que complica la construcción de un automóvil y, como consecuencia, reduce la rentabilidad de la producción.
La tecnología BlueTec se basa en una combinación de soluciones tradicionales y nuevas. El gas de escape ha comenzado a pasar por la resistencia de la mayoría de los vehículos diesel y el catalizador para "matar" el carbono. Luego, la inyección de escape se rocía con un reactivo activo AdVlue basado en urea (solución de amoníaco en agua). La mezcla resultante se coloca en un catalizador de elección especial (SCR), donde el amoníaco de AdBlue bajo la influencia de la catálisis a 250-300 ° C es eficaz en la reacción química de los óxidos de nitrógeno al "llevarlos" al nitrógeno y al agua. El resto de los componentes nocivos se están quemando aquí.
Con ventajas obvias, BlueTec no tiene menos desventajas obvias. El almacén de un componente AdLog requiere una capacidad distinta. El sistema en sí es complicado por la presencia de centros y autopistas adicionales. Además, el sistema es aún más lujurioso para la calidad del combustible y sólo puede funcionar en salazón con un contenido mínimo de azufre.
Otro problema muy relevante para Rusia: la solución de Adlue se mide a menos 11,5 grados. Por lo tanto, los ingenieros de BlueTec trabajan activamente en la mejora de los sistemas sin necesidad de utilizar urea. Hoy es la prueba y el refinamiento del filtro compuesto, catalizador de catalizador de platino y dos SCR-catalizadores exclusivamente para óxidos de nitrógeno. Actualmente, el sistema permite la utilización de NOx en los gases de escape de aproximadamente 5 euros.