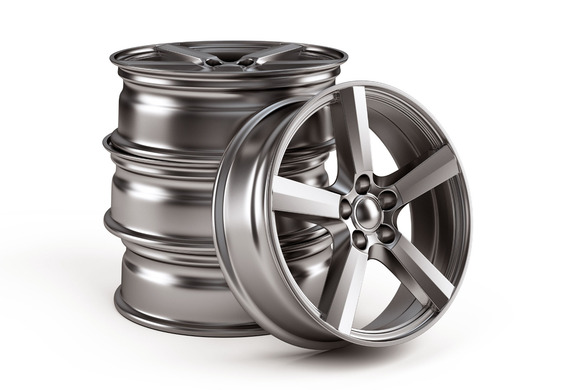
Nomination
Les disques durs sont faits d'alliages à base d'aluminium ou de magnésium, mais d'autres façons. Il comprend l'estampillage en vrac chaud dans des matrices fermées et le traitement subséquent-thermique et mécanique.
Dans notre pays, la production de disques forgés est la technologie de la construction aéronautique. Avec l'effondrement de l'URSS, de nombreuses entreprises de l'industrie aérospatiale ont cessé de recevoir des commandes de l'État. Pour survivre, ils ont commencé à s'adapter à la production de biens de consommation, y compris les disques automobiles.
Les disques forgés de la production nationale sont très respectés à l'étranger. Par exemple, un spectacle automobile en Allemagne en 2009 a été présenté par Bentley et Aston Martin sur les disques russes de M&K. Les disques forgés intérieurs auraient été plus populaires dans le monde si ce n'était "mais". Leur conception n'est pas la bienvenue. Il n'y a pas si longtemps, une lutte active contre ce problème est le début d'Atheforganisation. La société a conclu un contrat avec l'un des plus grands fabricants et accepte des commandes uniques pour le développement de modèles de disques forgés exclusifs. La vérité, le développement et l'exécution prennent beaucoup de temps.
Unité
Le matériau utilisé est un alliage de haute résistance et de plastique de type AV, qui a un deuxième nom pour "aéronef aluminium". C'est un alliage d'aluminium avec l'addition de cuivre, de silicium, de magnésium et de manganèse. Initialement, les cylindres ont un diamètre d'environ 20 cm. Ils sont coupés en morceaux, selon la taille et l'épaisseur des produits finis. Dans le magasin de presse de fonderie, ils se réchauffent et scinde la presse hydraulique: ils ressemblent maintenant à d'énormes crêpes de métal épais d'environ 50 cm de diamètre. Puis les talons sont réchauffés à 430 ° C, et l'embouti chaud est pressé contre eux, les rendant convexes, en apparence en ressemblant à des casseroles. Ensuite vient un autre échauffement dans le four et encore une fois par estampage pour donner le profil correct aux disques. Les marchandises finies sont envoyées pour contrôler la géométrie.
L'étape suivante est le traitement thermique. Il est nécessaire de faire les disques forgés de la force, de la plasticité et de l'élasticité, parce que la structure du métal devient méllotique et fibreuse. Le procédé répète exactement le traitement thermique des disques en fonte: ils sont injectés dans des fours en quelques heures, refroidis dans l'eau et artificiellement mis à l'âge pour éliminer les contraintes internes.
Ensuite, quelques morceaux de l'expédition sont envoyés pour le contrôle. Pour mieux voir les défauts de l'estampage, la surface du disque est plus brillante-elle devient plus légère. Un disque du lot est taillé et sculpté à l'extérieur pour un examen plus approfondi au laboratoire pour vérifier l'homogénéité de l'alliage, le contrôle de qualité du traitement thermique et la détection de la déformation. Particulièrement exposés au mariage sont les gouttes de pluie (centrale) du disque-ici la déformation est la plus complexe du point de vue métallurgique. Les propriétés mécaniques de l'alliage doivent également être contrôlées. Pour cela, les fragments sont placés dans une machine de rupture spéciale.
Si toutes les caractéristiques énumérées se trouvent dans des tolérances acceptables, le lot doit être accepté et usiné. Sur le lathe, la ferraille est enlevée et les trous nécessaires sont percés. Enfin, le disque est installé sur une fraiseuse où la conception programmée est coupée. Le chiffre qui est provisoirement mis au point par un programme informatique peut être laconique ou vicié-le principal est que la roue est capable de résister à une certaine charge. Dans certains cas, les disques sont encore polis.
Avantage et inconvénients
Les disques durs sont beaucoup plus puissants que les autres analogues. Ils sont meilleurs pour mener de petites grèves, et avec des impacts graves-comme un trou dans un trou-ne se fissurent pas, mais seulement. Ils présentent également une très forte résistance à la corrosion, qui permet de les traiter sans revêtement.
De plus, les disques de ce type sont les plus faciles à produire aujourd'hui.
Le principal inconvénient des faux disques est leur coût élevé. Le coût de la trousse dépasse le prix moyen des analogues estampées. Même les disques se trouvent dans une catégorie de prix inférieure.
Il y a un autre moins. Malheureusement, la suspension du véhicule sur lequel sont installés les disques forgés est portée très rapidement parce qu'ils ne prennent pas part au reflet des coups.
En outre, les disques forgés ont une ligne de dimension limitée. Par exemple, seule une usine en Russie produit 22 pouces (22) de pouce (22) de pouce (22) de pouce (22) de pouce (22 pouces), avec des presses plus faibles sur toutes les autres entreprises, ce qui ne peut que pousser les petits et moyens disques.
Malgré cela, de nombreux analystes disent que l'avenir est derrière les disques ouvrés. La demande pour eux augmente rapidement chaque année, car presque tous les indicateurs sont plus nombreux que le type de disque.