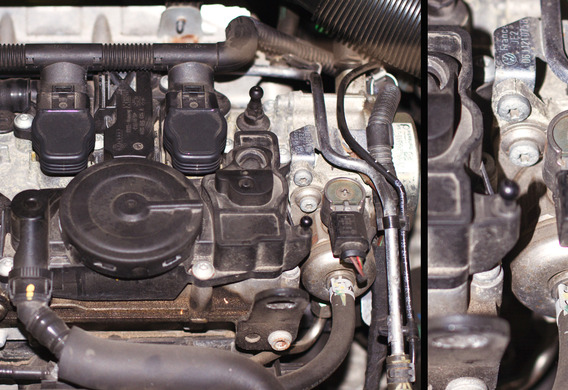
Le système de contrôle électronique de l'injection s'applique aux moteurs diesel et aux moteurs à essence. Lorsqu'il est monté sur un moteur à essence, le système d'injection avec un THLF dirigé par un électron est utilisé pour économiser et utiliser plus efficacement le carburant. Dans le cas du moteur diesel, en plus des facteurs susmentionnés, le système est en mesure d'obtenir une bonne sortie du moteur à une capacité supérieure à ce qu'il est dans les unités diesel. Histoire des systèmes d'injection électronique Histoire des systèmes d'injection électronique
Histoire des systèmes d'injection électronique
Le système de contrôle d'injection EPIC pour les moteurs diesel a été dirigé par Lucas à la fin des années 70. En ce moment, EPIC et ses variétés sont considérées comme les plus parfaites, puisqu'il est possible d'obtenir la combustion la plus efficace du carburant diesel. EPIC et ses modifications sont installées sur Citroën, Mercedes-Benz, Peugeot, Ford, Toyota et d'autres.
En général, dans le cas d'un système d'injection contrôlé par essence, la lettre "E" est ajoutée à l'abréviation à laquelle le moteur est modifié. La même ther au nom du moteur diesel, c'est l'utilisation d'un contrôle électronique. Par exemple, les véhicules Toyota Motor peuvent être équipés de 1HD-FTE, 2C-TE, AP-TE ou 1KZ-TE.
Qu'est-ce qu'un TDDG avec contrôle électronique?
Un certain nombre de moteurs modernes, à la fois diesel et essence, sont équipés d'une injection de carburant distribuée avec contrôle électronique. Le système d'injection directe pour les moteurs à essence et tous les moteurs diesel est basé sur le principe de préaccumulation d'une certaine réserve de carburant à haute pression. À l'avenir, ce carburant est facturé en plusieurs lots, dans la plupart des cas, directement dans le cylindre, pendant la compression et l'accident vasculaire cérébral.
Une pompe à combustible à haute pression ou un DDP est utilisé pour créer la pression dans les systèmes d'injection. Dans les systèmes les plus avancés, le DDP, comme tous les autres composants du système d'injection, fonctionne sous le contrôle de l'électronique de façon à ce que tous les paramètres puissent être contrôlés avec une grande précision. Cela conduit à des taux plus élevés de puissance et de rationalité de la consommation de carburant que pour les moteurs équipés de systèmes TDDP conventionnels.
Les pompes à commande électronique peuvent être utilisées comme diesels avec une caméra à tourbillon, où le mélange du combustible avec l'air se produit, c'est-à-dire que le mélange est créé et que les moteurs d'injection sont directement dans les cylindres. Les différences dans la conception des moteurs ne jouent pas un rôle particulier-la différence n'est que dans la pression du carburant de rampe, dont la création et le maintien sont effectués par le DDP. Si le moteur viscéral est pressurisé de 350 kg / cm2, les moteurs à injection directe doivent avoir une pression pouvant atteindre 1 000 kgs / cm2.
TDDs contrôlés par voie électronique de différentes générations
Les pompes sont divisées selon le principe du piston. La première génération (pompes Bosch VE) est équipée de pompes de transmission et de seconde génération (Bosch VR, Lucas DPC, Luas DPS)-dispositif de came interne. Quelle était la raison d'être des nouvelles générations? Le fait est que la pression maximale dans le système de pompe VE n'est que de 150 kgs / cm2, et que la poursuite de l'augmentation est limitée par la conception de l'unité. Par conséquent, avec l'avènement d'une meilleure unité interne, la deuxième génération de Lucas DPC et les similaires sont apparus.
En raison de l'application du nouveau type de transmission, le HFD avec le mouvement radial des plongeurs est capable de créer une pression plus élevée-jusqu'à 1000 kgs / cm2.
Réglage des paramètres d'injection sur les systèmes avec un TNT contrôlé par voie électronique
Alors qu'auparavant, les DHB mécaniques n'étaient utilisées que pour créer la pression nécessaire, les TDD modernes commandés par voie électronique, ainsi que les machines à doser, sont responsables à la fois de la quantité de combustible injecté dans un cycle et du changement du mode de fonctionnement du moteur dans différentes conditions routières.
Les TDD électroniques modernes sont appelées pompes par répartition.
L'unité de commande électronique, qui est responsable du fonctionnement du DDP, reçoit des signaux de différents capteurs: les températures de l'oB et du combustible, la fréquence de l'arbre de roue, la position du capteur, le capteur de vitesse, le capteur de vitesse, la position de la pédale d'accélérateur et d'autres. Tous ces signaux sont comparés au programme de blocage et un signal est donné au DDP qui fournit la quantité désirée de carburant aux injecteurs et l'UV optimal (angle d'injection), en tenant compte de la charge actuelle du moteur.
La régulation du flux de combustible est produite par l'éveil de la posologie. La vanne est une vanne de commande de vanne. L'injection et la transmission de l'aiguille et, par conséquent, la puissance du flux à travers le coupleur de combustible, sont dirigées par un moteur électrique en marche ou un électro-aimant avec un noyau de retournage. Selon le signal de l'unité de commande, il peut ouvrir ou fermer la valve avec une grande précision. Le moteur servo a un taux de réponse élevé, ce qui assure la commutation rapide des modes d'alimentation en carburant en fonction de la charge sur le moteur.
L'avance d'injection (un paramètre similaire à l'angle d'allumage dans les moteurs à essence) est contrôlée de la même façon par une vanne électromagnétique. La vitesse de l'angle de la roue sera optimale pour différentes charges et vitesses de rotation. Par exemple, l'angle d'inactivité dans la zone de 800 /min doit être de 3 °, à 1000 tr / min, 4 ° et ainsi de suite. Pour cette raison, un changement dynamique du moment de l'injection est organisé dans les systèmes d'injection électronique. Le moment de l'injection doit être réduit lorsque la charge sur le moteur est réduite et augmentée par ordre croissant.
L'une des buses est équipée d'un détecteur de marque d'aiguille. Le signal doit être transmis à l'unité de commande du moteur. Le moment de pointe du capteur sert de point de référence pour le contrôle de l'angle avant. Sa valeur est comparée aux données de la "carte" (table des valeurs) qui contient des données pour différents modes de fonctionnement du moteur, selon l'angle choisi.