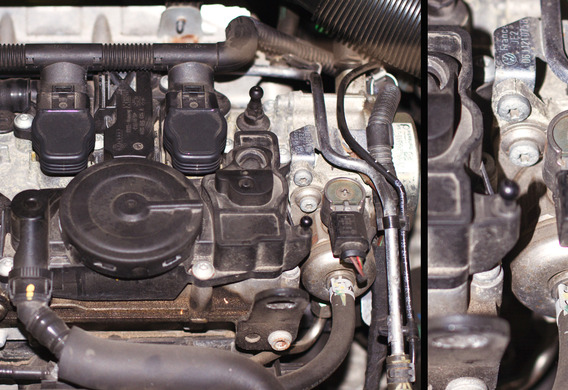
The electronic injection control system applies to both diesel and petrol-fuelled engines. When fitted to a gasoline engine, the injection system with an electron-driven THLF is used to save and make more efficient use of fuel. In the case of diesel engine, in addition to the above mentioned factors, the system is able to obtain a good output from the engine at higher capacity than it is in diesel units. History of e-injection systems
History of e-injection systems
The EPIC injection control system for diesel engines was run by Lucas at the end of the seventies. At the moment, EPIC and its varieties are considered the most perfect, since it is possible to achieve the most effective combustion of diesel fuel. EPIC and its modifications are installed on Citroen, Mercedes-Benz, Peugeot, Ford, Toyota and others.
In general, in the case of a petrol-controlled injection system, the letter "E" is added to the abbreviation to which the engine is modified. The same lither in the name of the diesel engine means the use of an electronic control. For example, Toyota Motor vehicles can be equipped with 1HD-FTE, 2C-TE, AP-TE, or 1KZ-TE.
What is a TDDG with electronic control?
A number of modern engines, both diesel and petrol, are equipped with a distributed fuel injection with electronic control. The direct injection system for petrol-fuelled engines and all diesel engines is based on the principle of pre-accumulation of a certain high pressure fuel reserve. In the future, this fuel is being charged in several batches, in most cases, directly into the cylinder, during the compression and working stroke.
A high pressure fuel pump or a DDP is used to create the pressure in the injection systems. In the most advanced systems, the DDP, like all other components of the injection system, runs under the control of electronics so that all parameters can be controlled with high accuracy. This leads to higher rates of power and rationality of fuel consumption than for engines equipped with conventional TDDP systems.
Electronically controlled pumps may be used as diesels with a whirlwind camera, where the mixing of the fuel with the air is occurring, i.e. the mixture is created and the injection engines are directly into the cylinders. The differences in the design of the engines do not play a special role-the difference is only in the pressure of the ramp fuel, the creation and maintenance of which is carried out by the DDP. If the visceral engine is pressurized by 350 kg/ cm2, the direct injection engines shall have a pressure of up to 1,000 kgs/cm2.
Electronically controlled TDDs of different generations
Pumps are divided according to the principle of the plunger. The first generation (Bosch VE pumps) is equipped with end-cam transmission and second generation pumps (Bosch VR, Lucas DPC, Luas DPS)-internal cam device. What was the rationale for changing generations? The fact is that the maximum pressure in the VE pump system is only 150 kgs/cm2, and further increase is limited by the design of the drive. Therefore, with the advent of a better internal drive, the second generation of Lucas DPC and the like have appeared.
Due to the application of the new type of transmission, the HFD with radial motion of the pluners is capable of creating a higher pressure-up to 1000 kgs/cm2.
Adjusting the injection parameters on systems with an electronically controlled TNT
Whereas previously the mechanical DHBs were used only to create the necessary pressure, modern electronic-controlled TDDs, together with the so-called dosing machines, are responsible for both the quantity of fuel injected in one cycle and the change of engine operating mode under different road conditions.
Modern electronic TDDs are called pay-as-you-go pumps.
The electronic control unit, which is responsible for the operation of the DDP, receives signals from different sensors: the temperatures of the oB and the fuel, the frequency of the wheel shaft, the sensor position, the speed sensor, the speed sensor, the accelerator pedal position and others. All these signals are compared to the tuning block programme and a signal is given to the DDP that provides the desired amount of fuel to the injectors and the optimum UV (injection angle), taking into account the current engine load.
Regulation of fuel feed is produced by the dosing mousing. The muft is a valve control valve. The injection and transmission of the needle and, therefore, the power of the flow through the fuel coupler, is run by a step electric motor or a electromagnet with a turning core. Depending on the signal from the control unit, it can open or close the valve with high accuracy. The servo motor has a high response rate, which ensures the rapid switching of the fuel supply modes according to the load on the engine.
Injection advance (a parameter similar to the ignition angle in petrol engines) is controlled in the same way by an electromagnetic valve. The speed of the wheel angle will be optimal for different loads and rotational speeds. For example, the angle of idle in the area of 800 /min shall be 3 °, at 1000 rpm, 4 ° and so on. For this reason, a dynamic change in the injection timing is organized in electronic injection systems. The injection timing should be reduced when the load on the engine is reduced and increased in ascending order.
One of the nozzles is fitted with a needle mark sensor. The signal shall be transmitted to the engine control unit. Peak momentum from the sensor serves as a reference point for the control of the forward angle. Its value is compared to the data of the so-called "map" (table of values) that contains data for different engine operating modes, depending on which angle is chosen.