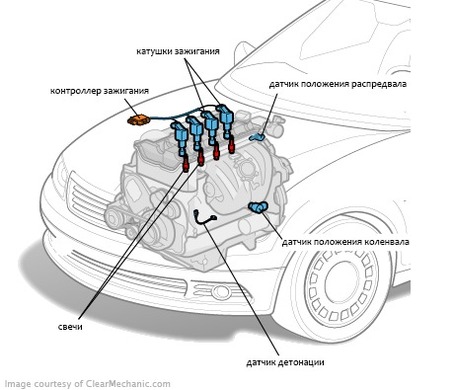
The ignition engine is a mechanical device designed to transmit the current high voltage from the ignition coil to the candlelight, alternating in a certain order. Massively applied in the time of the contact ignition and the carbusts ' injection systems. History of appearance
History of appearance
The first functional contact spark pluter, which included a distributor, was developed by [ [ Charles Kettering]] of the company Dayton Engineering Laboratories Co. (Delco). It was first installed in Cadillac cars of 1910 model year and was perceived as a technical miracle.
Ignition Distributor
Inside the closed compartment cover the rotor shaft has been installed. The shaft is made of dielectric runners, insulated from the metal shaft and body of the car ("mass").
It's enough for the ignition system to buy candles enough. Thirty years ago, the list of costs consisted of a lid, a runner, and a contact group of the ignition
The allocator is given in the movement of the gear fortified at the engine crankshaft. The gear is included in the cordon with the other six complex form at the end of the introduction of the ignition engine. During the development of the engine and the operation of the cars it became clear that the allocator very "does not like" water. To protect it from moisture, the shaft has been made as long as possible so that the valve body is positioned as far away from the road as possible.
The role of the cover in the allocator
The lid of the allocator shall alternately transmit the high voltage current from the secondary coils of ignition through the high-voltage wires on the candle.
The lid of the allocator is made from material that does not produce current. Metal contacts-central and lateral electrodes have been pressed into the casing of the cover. The number of lateral electrodes corresponds to the number of candles. From the outer side of the cap to the central electrode, a wire is attached to the ignition coil, and to the side-high voltage wires going to the candlelight. The central contact, located inside the cover, is fitted with a sticker with a spring-loaded contact from the graphite that transmits the voltage to the central contact of the ignition engine.
What's a jogger?
The ignition engine or "errand" engine is a plastic part attached to the allocator shaft. It serves as the holder for the central contact, which is connected to the lateral contact through the resistor, an overwhelming interference. The rotor has been rigidly fixed at the allocator shaft. When the shaft of the shaft is rotated, the rotor's lateral contact is in contact with the side terminals of the cover, passing the high voltage wires to the high voltage lines, and then by candlelight (the "spark" thus appears-a short term high voltage discharge compressed in the combustion chamber mixture).
Eight high-voltage contacts have been introduced in the Twin Spark plugs lid that was promoted by Fiat for a four-cylinder engine. The candles were also 8
The ignition control system is attached to the valve body using latches or bolts. A vent shall be provided in the lid to prevent condensation.
Load Balancer Principle
The metal base of the johnman has a high voltage wire. The contact with the rebalancer is implemented as a spring-loaded tray that can be used continuously for the base of the thumb, but does not interfere with its rotation.
On the shaft of the rotor, there is a protrusion or a doll that, when rotating, pushes the mechanical device lever, which is referred to as the breaker. When the collapse of the balancer is broken by the circuit breaker's contacts, a high voltage current is displayed in the ignition coil, which is then heard in the candle. By the way, in the automotive textbooks the allocator is officially known as "dispenser-breaker".
However, this is not all the functions that the balancer does. It provides a mechanism for the timing of the ignition (of the parameter necessary for fuel-air mixture combustion in each cylinder at the optimum compression of compression, that is, slightly ahead). The ignition timing mechanism is attached to the principle of the centrifuge-a set of motors on movable levers are attached to the engine shaft, which influence the plate with the circuit breaker and, by moving it, increase the spark timing when the shaft of the engine is dizzled to high speed. In addition to the centrifuge, a vacuum correction tank is fitted with a inlet manifold, which also adjusts the ignition timing.
The repair of the mechanical finder's centrifugal mechanism can be unremount by a Swiss watch technician. Therefore, the Distributor usually changes the whole
In addition to these elements, a capacitor connected in parallel to the circuit breaker is installed in the tower. Its task is to prevent the formation of sparks on the contacts of the circuit breaker, which significantly reduces their carrots and wear.
In the seventies, the mechanical circuit breaker is gradually disappearing from the structure of the allocator because of the general unreliability of the structure. In relatively modern carburetors it was replaced by a Hall or an optical sensor. The use of these devices has led to the implementation of a contactless circuit breaker, which is simpler to design. With the distribution of the Hall sensor, it was no longer necessary to keep track of the condition of the circuit breaker, the pressure spring, and the roll on the shaft-possibly the most capriciating mechanism in the entire automotive design.
Injector ignition
At the early stage of the development of the controlled electronics of distributed injection systems, the mechanical allocator, although in simplified form, remained a part of the ignition system for a long time before the distribution of the electronic high-voltage switches. Most of the distributors used in the ignition engine system have already been deprived not only of the mechanical flushing of the contacts but also of the vacuum-proofing of the ignition timing. In the ignition system design, the electronic engine control unit took over the engine. The application of the computer made it possible to make advance more accurate and change the settings in real time, based not only on the speed of the wheel rotation, but also on a number of other parameters, such as the temperature sensor reading, the volume of the combustion chamber, its temperature, and so on.
Spark plugs have become more reliable as they remain, in fact, only the retractable and oxidizing latches of the allocator's rotor, its electrode, and the contacts that are fitted to the lid.
Sometimes it turns out that it is impossible to buy a new dispenser for not too much "ancient" machine. If this happens, you don't need to despair-the ignition system can be completely rebuilt.
In the future, the mechanical allocator completely disappeared from the car design, and modern models can only be used to reduce costs.
Spark plugs management issues
All inside parts must be clean and dry for reliable operation of the allocator. The cover shall be firmly attached to the shell and shall not permit any moisture missing in the atmosphere. However, the service access cover does not have a complete leak-tightness, and condensation may occur under the cover due to a sharp change in the weather. There are known cases where the engine has not been driven because of condensation. If this happens, the cover needs to be dried (sometimes it is enough to remove the moisture on the cloth). The cover should be regularly checked for cracks and the condition of the electrodes. From permanent and non-tight contact they form a tgar, which can be cleaned with a small file or sandpaper. You can use sandpaper, but before you install the cover, it should be carefully cleaned from the abrasive particles. If the rotor's contact showed signs of trouching, it should also be cleaned, and if the edge of the electrode was strong, the thumb should be replaced.
Often in the dispenser, the depressed resistor is burned. This failure causes the engine to be unable to start. If it did, it should also be replaced.