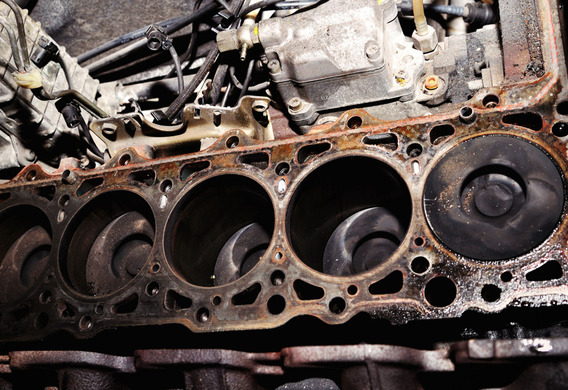
The creation of the most light and powerful engine is a priority task for engineers of all car companies, which they have been trying to solve for more than a century. The real revolution was the emergence of fully aluminum-made engines. However, the use of this material has created a new challenge for developers-how to create durable cylinders in the aluminium block? The best solution was to use the shell casing that was actively used to create engines for motorcycles that do not have a common cylinder block. Types of shell casings and requirements
Types of shell casings and requirements
The casings must be very strong and tight, because in the case of the aluminium block, it only plays the role of the shell in which it is held. It has to stand against heat, pressure and wear on its own. Therefore, the casings must have high durability, high corrosion resistance, heat resistance and strength. Depending on the design of the engine, the casings are divided into "wet" and "dry". The essence of this term is directly related to the engine water cooling system.
The "Wet" is the most widely used cartridge, as it is excellent to solve the problem of heat dissipation
"Wet" casings
"Wet" is a shell casing whose external surface is washed by a cooling liquid circulating in the system of channels that break the thickness of the cylinder block. This system is called a "water jacket" and serves to balance the heat from the cylinder block. In the area of the installation of the casings, the cooling liquid "goes to the surface" so that the walls of the shell are washed directly. That's why the type of cartridge is called wet. The cylinder block with wet shells provides the best dissipation of heat, so the "wet" cartridge cases are very wide. They are used in cars Volvo, Renault, GAZ-24, Moskvich and others.
The sealing between the shell and the block is achieved by a copper spacer between the shell casings and the plane of the unit
Renovation of engines equipped with "wet" shell casings is extremely simple-a new pair of piston casings are installed in the unit, which do not need to be further developed. It is not even necessary for the capital to remove the engine, and it can be performed even in the field.
"Dry" casings
The "dry" cartridges are stacked in the body of the cylinder and have no direct contact with the coolant. Some producers prefer to make aluminium blocks with non-replaceable bullet casings. In this case, the casings are strengthened in the form of casting, which is later filled with molten aluminium. The resulting blocks of cylinders are no different from the conventional iron iron. If necessary, the casings of the shell are staunched and briskles as normal cylinders. This technology is used for the production of Volkswagen, Land Rover, Honda, Audi, Volvo and a number of others.
"Dry" casings are worse than heat, but their use makes it possible to give a block of cylinders monolithic stiffness
The use of the shell removes the limit from the amount of remontov that the unit can withstand. In theory, this can be done for an unlimited number of times, although in fact it is not necessary, since the body of the car, unfortunately, is not. For example, no more than 3-4 manufacturer-specified repair pistons shall be used for a normal block without cartridge cases. This limits the number of possible repairs. When the last repair and the cylinder is no longer liable to be crushed, it is "out" the shell casings, which again raise the block's resource into several repairs.
Installation of cylinder casing
The internal surface of the cylinder is static and slicing carefully before the pressure of the cylinder, the same treatment shall be subjected to the outer surface of the cartridge for the density of the landing into the cylinder. Then the shell casings, which usually have a stubborn edge in the upper part, are pressed into a squatted cylinder with a motive of 0.03-0.04 mm.
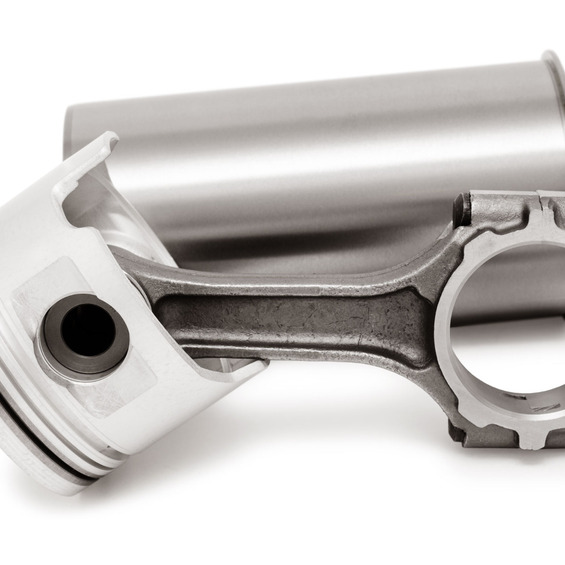
"Wet" casings fully "ready for use". There is no need to handle the internal surface of the inner surface after the assembly has been put into the cylinder block. Dry shell casings are generally needed after installation.
The casings are stayin and they are chonguing severely under a certain group of pistons. Each piston is measured and the shell of the shell is crushed. After such a fitting, the piston shall be marked on the cylinder and shall not be installed in other cylinders. By the way, it is recommended to purchase the so-called "PSP" from the hyper-mounted engine, selected from the factory conditions with bundles of shell casings, cylinders and fingers.
An exception to this is the Japanese company Isuzu, which produces engines where the block is equipped with steel and coated steel casings with porous chromium that do not require mechanical handling.
In the Isuzu engines, the casings are placed in a unit without draught and are held in the body by means of a fastenes fastenings over the top of the cylinder block.
Hillings in air-cooled engines
For air-cooled engines, cylinder shells are made in the form of a motorcycle, with cooling ribs. As the cylinders are to be cooled by the airflow, they cannot form a unit and are installed on the engine as separate parts.
The casings are attached to the crankcase (through copper gaskets) by means of low pins through a special support flange, or by means of an anker spy, passing through the entire cylinder head. The head shall be fitted with these stiletters and shall be tightened normally, thus pressing the cylinders to the crankcase and ensuring the sealing of the cylinders.
Motor-cycle engines with air cooling and became "donor" to the world of motor vehicles
For air-cooled engines, cylinders are made of either a single metal (mono-metal) or two metals (metal).
Mounmetallic air cooling cylinders are mainly performed from cast iron, sometimes from steel or light alloys.
Bimetallic cylinders have also been made of iron or steel, and on top of the hull are aluminum ribs.
Deficiencies in air-cooling units
Engines with hot air cooling are very susceptible to temperature and overheating "suffer" from the release of cylinder studing of cylinder s in the aluminium block. This leads to the extraction of the stiletto and the destruction of the threads, which weakly causes the jacket of the shell and causes depressurization and loss of compression. The attempt to connect the connection ends with the full exit of the carpeter's carcasses and subsequent repairs. In other words, it is not under any circumstances to allow the aluminium engine to be overheated.