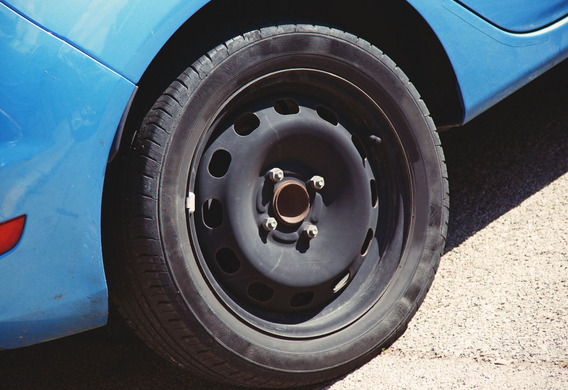
Stambed disks are not lastivious in operation and are sufficiently strong. The design is simple: the factory press-form throws the rim and the circle, then they are welding together. Such discs are made of direct steelmaking discs, therefore they are not liable to blows or deformations-the solid metal is resistant to heavy loads.
Today these are the cheapest and most common automobile discs
If the disc bent, it's easy to get out. This can be done independently by a regular hammer or at a workshop where there is a special device. Stamps have a very high wear resistance. To avoid corrosion, the surface of the finished disks cover the enamel, chromium, electron coating, or the special powder layer. There are also technologies for the production of tar discs with the addition of magnesium, which ensures corrosion resistance.

Stambed Disk History
The history of the disks is more than a hundred years old. They began to be manufactured for the first wheels with rubber tyres back in the early 20th century, when people decided to abandon the spokes in favor of tyres and disks.
One time of [ [ stamp]] discs made in Russia were even installed on cars manufactured in Japan
Today these are the cheapest and most common automobile discs. There are many serial cars worldwide. At one time, the discs manufactured in Russia were even installed on cars manufactured in Japan. The fact is that we have very well-developed conversion technologies, when the defense industry is being rebuilt for peaceful purposes. Products manufactured in this way have a very high quality. At the same time, the cost of the strain of the disk drives is extremely low.
Pledge and floppy disks
One of the merits of the disc is their plasticity. When they hit a hole or when they hit, they don't break, they don't crack, they don't burst, they don't burst, they don't break, they don't break. The tires and suspension do not suffer; after a recovery, the disk looks the same as before and can still be in service for a very long time. Stambed disks are well suited for domestic machines.
The biggest shortage of tar disks is their weight, which affects the dynamics of the machine. Hard disk, like a giant flywheel, is hard to launch and it's hard to stop. The car is slowly catching up and does not react well to braking. The mass of the car is growing-the mass of everything under the suspension (the wheels, parts of the brake system and the parts and parts) Due to this suspension, the movement becomes less comfortable. Also, the weight of the drives increases the fuel consumption.
The downsides of the stamped drives include their unattractive appearance. They all look the same, and they don't like motorists at all. But, on the other hand, the owner may not worry that one day he will find his car "rawled"-there are no cases of theft of such discs. And to improve the aesthetic qualities, you can install plastic caps on discs that imitate casting.

Another disadvantage is the poor painting of the strain of the strain that results in rust. If you purchase, you need to carefully examine the disc for the absence of scratches, see if the paint has not been bought. It is best to choose models that are covered with powdered enamel: usually it is bright and white. It's sprayed by electrical stress. This coating shall cover the metal surface of the disc and shall not allow moisture to penetrate into operation. In addition, the powder enamel is long kept and protects the disks in the winter of salt and other reagents. The discs that are not coated with any corrosion resistant coating need to paint every year-then they will last for a long time.
The next minus-disks must be regularly washed, especially in autumn and winter, when there is a lot of snow and dirt on the roads. In other case, outside noise, vibration of the body and rudder may be heard during the movement in the passenger compartment. The fact that protective caps are often blindly flinching or burst in favor of the strain of the disk drives are also said to be unhelpful.