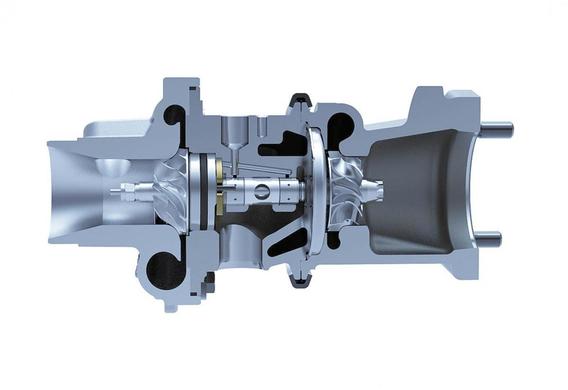
History of the invention of a turbied gasoline engine
The possibility of increasing the capacity, not increasing infinitely the working volume, has been interested in engineers since the advent of internal combustion engine. The solution seemed to lie on the surface: it is necessary to make the engine's "breathing" more efficient, that is to achieve better fuel-air tightness. This may provide additional air supply, which means that it must enter the cylinders not due to dilution, but forced under pressure. The additional volume of air will result in a more complete combustion of the fuel, respectively, and the capacity resulting from the "mini-explosion" of the mixture in the cylinder will increase.
However, the development and deployment of tourism technologies has been slow. Originally, turbochargers were used for large ship and air power installations, and the first vehicles with turbocharged engines became the trucks.
The Swiss Machine Works Works auer has started to manufacture these facilities since 1938. In the early 1960s, the first cars with turbines appeared on the American market. It was Oldmobile Jetfire and Chevrolet Corvair Monza. However, these models were neither reliable nor resilient.
Popular turbocompressors began to be massively installed in sports cars in the ' 70s of the 20th century. However, they were not widely distributed in the "civilian" automobile industry, which was prevented by too much fuel consumption, which distinguished turbo jet engines of those times. In the context of the oil crisis of the 1970s, this parameter was more important than all others.
The device and the operating principle of a turbated gasoline engine
The working principle of a turbocharged petrol propulsion system is the use of a special compressor for extra air in the engine cylinder.
Due to the improvement of the filling of the cylinder, the fuel efficiency is increased, the average effective pressure of the cycle is increased and the power of the engine increases. Turbocharged turbocharged is used gas, the energy of which is used for useful work.
The modern turbocharger includes:-the bearings;-turbo wheel;-the transfer valve;-the turbine hull;-the oil-channels;-the shaft of the rotor;-the compressor unit;-the compressor unit;-Pneumonia transfer valve.
The bearing of the bearings is rotor: a shaft with rigid fixed turbine and blades. Rotating the rotor at the slide bearing. Their lubrication and cooling shall be carried out by engine oil from the engine lubrication system. Cooling liquid channels may be used to further cool the bearing body.
The turbine body, like the entire compressor, is in the shape of a snail. The turbine tube is connected to the exhaust pipe, and the compressor is connected to the intake line.
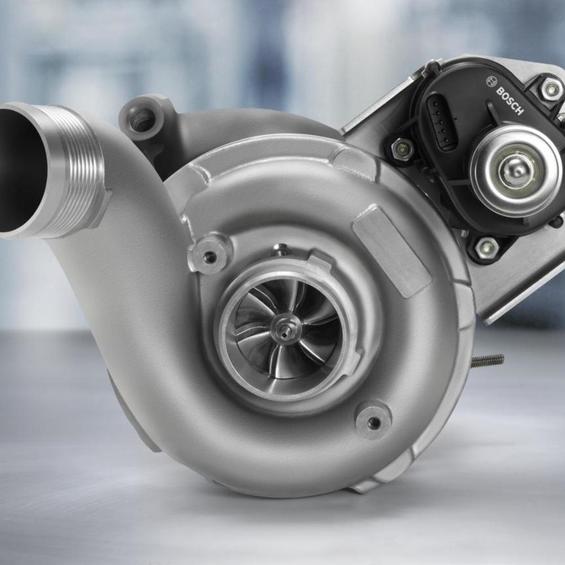
The processed gases enter the turbine and unwind the turbocharger's rotor, giving its energy. Then they come into the silencer through the reception pipe. Compressor wheel and scapular turbine wheel are placed on one shaft. By rotating the rotation of the turbine, the compressor wheel will pump air out of the air filter and, naget it, shall be fed into the engine. At the same time, the compressor, depending on the degree of boost, is able to increase the air pressure by 30 %-80%. By means of turbocharged, the same engine capacity may take a working mixture in more. Therefore, when it is burned, the power is increased by 20% to 50%! The use of exhaust energy makes it possible to significantly increase the efficiency of the engine.
Advantage and disadvantages of a turbied gasoline engine
The main advantage of a turbi-based gasoline engine is its comparative strength. It is understood that, with the same volume, the turbo engine produces 40% more power than "atmospheric". The undoubted dignity of this type of power plant is considered to be a reduced discharge into the atmosphere of harmful substances.
However, turbized gasoline engines have a number of drawbacks. In order to reduce the resulting detonation, it was necessary to reduce the compression of the engines in cylinders. Fuel quality requirements have also increased-only high-octane stamps are suitable for this type of propulsion system.
The design had to add an intercooler-intermediate chiller of the injection air, so that after heating in the turbine, its density did not decrease. The high temperature that occurs during the operating cycle dictates a strict selection of materials for the production of the exhaust system, compressor units and turbine blades. But all these problems do not interfere with turbocharged gasoline engines to become increasingly popular among car enthusiasts all over the world.