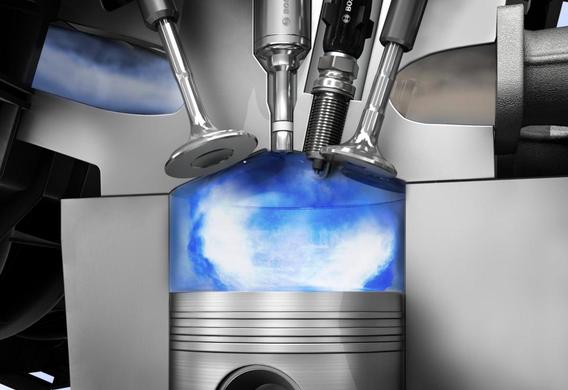
The device in which the high pressure fuel pump is combined with the nozzle, is called a power supply with pump-injector. History of inventions
History of inventions
Most sources claim that the engine-nozzles in production engines are in the mid-1990s, but there is information to allow other conclusions to be drawn.
Since the invention of the high pressure fuel pump by Robert Bosch, the development of the fuel equipment has gone on the way to improving the TDDP. In Robert Bosch's scheme, all the nozzle is feeding one common pump. In 1938, however, the world's first serial diesels with a system of power pump-injectors were built in the US by the company Droit Diesel owned by General Motors.
Pressure at pump-nozzle system is so strong that when a jet of fuel leak, the fuel can "cut" at the same time, clothing and skin on the arm
At the same time, the USSR actively worked on the creation of own fuel equipment for trucks. But after several unsuccessful attempts, it was decided to buy a license for a well-proven system during the tests of the 3-71 series Diesel Diesel series 3-71 and to establish it in Yaroslavl. The negotiations began in 1939, but the process was delayed first because of Finnish and then the Great Patriotic War.
It was only in 1945 that the plant produced the first machines and equipment for the production of American motors. In 1947, the first four-cylinder, twin diesel engines of Apple 204 with a power system with pump-nozzle system were released. This engine, as well as its six-cylinder analogues, with some refines were produced before 1992.
In 1994 Volvo produces its first European truck FH12 with pump-injector. Following the Swedes this power system appears on Scania and Iveco.
Pump-injectors are often destroyed by the pump at the diesel engine block
In the segment of touring cars the championship in the development of motors with pump-injectors belongs to Volkswagen. In the company's cars, diesel engines with injectors appeared in 1998.
Mechanical pump-injector
The injector shall consist of a high pressure fuel pump and a spray unit in the same shell. The DDP is located in the upper part of the lower house. The pump shall normally be placed under the valve cover and is not visible from the outside. The characteristic of the location is that the pump is activated by means of additional couchings provided for in the distribution shaft.
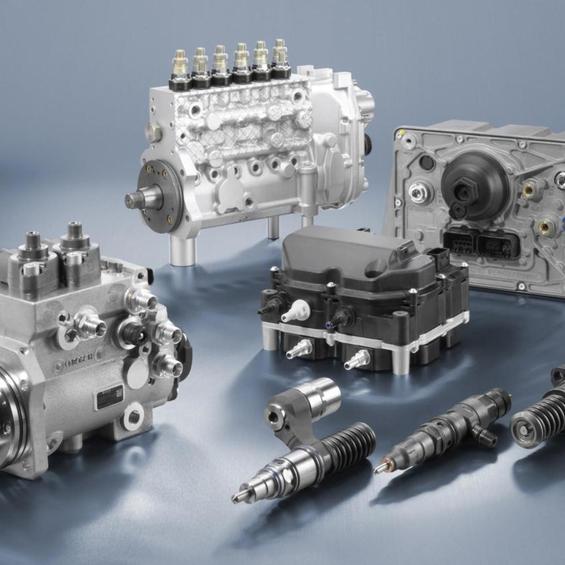
The principle of the normal mechanical pump-nozzle is quite simple. The chink pushed the plunger over the lever, the injector-injector. The pressure increases sharply when a sprayer is raised and the fuel goes into the combustion chamber when a certain value is reached. Mixture is ignite, and the expanding gases are pushing the piston. Electronic pump nozzle
Electronic pump nozzle
Modern electronic pump-injector work is somewhat different. The pressure is also created, as in mechanical, with the help of a plunger, but the moment of injection runs the electronic engine control unit. The number of fuel feed required can be up to 10 per stroke in the three main phases. The first is the preliminary injection, when a small portion of the fuel is supplied to the cylinder, for the preliminary heating of the combustion chamber and the best ignition of the incoming trace, the second, the main portion. The third phase is for burning non-burnt fuel and heating (regeneration) of the particulate filter.
The minimum cost of the pump is 18 thousand rubles for VW Passat in 2006
To ensure accurate dosing of each piece of fuel and to provide multiple injectors, an electromagnetic valve is used, which controls the lifting of the sprayer needle.
Advantage and disadvantages of pump-injector
The pump-out pump, unlike the Common Rail, allows injection of fuel under pressure of more than 2000 bar. As a result, fuel is sprayed more efficiently, so it burns more than half. Therefore, the engines with pump-nozzle are distinguished by their high unit capacity, economy and environmental performance.
In addition, engines with such a injection system work quieter than their counterparts with the Common Rail or the mechanical DDP with mechanical nozzle. In addition, the injector injection system is much more compact.
However, the cons of this system are no less serious. The most important is the requirement for pump-nozzles to fuel quality. Water, mud and surrogate fuel are lethal for them.
The second serious shortfall is the high cost of the pump-injector. The repair of this precision site is difficult to repair outside the factory conditions. Therefore, owners of vehicles with such a power system have to purchase new injector pumps.
Operation and maintenance of pump nozzle
The most common problems with pump-injector are related to the wear of the valve unit and the spray nozzles. The reason for the failure of these sites is primarily because of the poor quality of the fuel and the misuse of the vehicle with the system.
Several simple rules must be observed in order to prolong the life of the injector pump. First of all, you only need to get gas on the validated gas stations.
At the end of the 1990s engines with pump nozzle occupied 20% of the fuel market of European diesel engines
Second, do not in any case contribute to the tank with pump-injector petrol, kerosene, brake fluid, and other "kamazzovs" to bring the summer salt to the freezer of winter.
Third, fuel filter replacement needs to be reduced. It is possible to establish only original manufacturers allowed by the manufacturer. Because analogues often do not provide the required level of filtering.